3D WELDING VISION SYSTEM MARKET REPORT OVERVIEW
The global 3D Welding Vision System market size was 359.81 million in 2024, and the market is projected to touch 562.43 million by 2033, exhibiting a CAGR of 5.09% during the forecast period.
The global 3D welding vision system market has been growing quite rapidly due to the increased penetration of advanced automation technologies in various welding processes by different industries. These systems mainly contribute to greater accuracy in the welding process while reducing material wastage and enhancing the overall productivity index. This 3D image-based and real-time analytics systems can help with weld monitoring in detailed resolution and also maintain quality control over the welding process. Industries, such as automobiles, aerospace, construction, and manufacturing, have started using such systems more than ever before as they make it easier to tackle complex welding activities. Additionally, the growing desire for Industry 4.0 and smart factories is furthering the demand because companies seek ways to make their operations more efficient and minimize idle time.
COVID-19 IMPACT
3D Welding Vision System Market Had a Negative Effect Due to By Increasing disruption in global supply chains During COVID-19 Pandemic
The global COVID-19 pandemic has been unprecedented and staggering, with the market experiencing lower than anticipated demand across all regions compared to pre-pandemic levels. The sudden market growth reflected by the rise in CAGR is attributable to the market’s growth and demand returning to pre-pandemic levels.
During the COVID-19 pandemic, the 3D welding vision system market took an initial knock. The demand declined more sharply than before, as global supply chains were disturbed, factories shut down, and industrial production slowed due to curtailment of manufacturing activities because of lockdowns and other restrictions. At the same time, the pandemic helped the industry reposition itself for a new order that will prioritize automation and touchless operations rather than relying heavily on manual methods. As companies moved to reduce human intervention and improve operational resilience, investments in automated solutions, including 3D welding vision systems, began to accelerate. The post-pandemic shift toward automation was driving a recovery faster than expected, with demand picking up even more than before, as manufacturers turned to technologies that made their operations more efficient, precise, and safe. This trend reflects the role of the market in the more widespread adoption of Industry 4.0 practices across industries.
LATEST TREND
"Implementation of AI-Powered Welding Vision Systems to Drive Market Growth"
Integration of AI and ML with 3D welding vision systems is the most prominent trend in the market. This technology has led to more sophisticated defect detection, predictive maintenance, and real-time adjustments in the welding process. Manufacturers also launched compact and lightweight 3D vision systems, which could easily be fitted onto existing welding robots, improving flexibility and efficiency. Besides, the emphasis on sustainable manufacturing and energy-efficient solutions propels further innovations in this sector.
3D WELDING VISION SYSTEM MARKET SEGMENTATION
By Type
Based on Type, the global market can be categorized into Welding inspection, Weld seam tracking & Others:
- Welding Inspection: Welding inspection systems play a major role in critical applications to assure weld quality and integrity. These use 3D imaging technologies, giving detailed visual and dimensional analysis of weld joints with defects like cracks, porosity, and undercuts. For instance, in aerospace, automotive, and construction industries, they are more widely used because the quality requirement is very strict, and defects would lead to failure or complete breakdown in operations. These systems will most likely reduce human failure risk, increase productivity, and maintain adherence to international safety standards. A growing need by businesses across sectors for the automated quality control processes is likely to further increase the demand for welding inspection systems.
- Weld Seam Tracking: The purpose of weld seam tracking systems is to make sure that welding operations are very precise and in accordance with the path followed during automated welding. Advanced sensors and 3D cameras continuously monitor the position of the welding torch to adjust it so that the welding operation remains as consistent as possible, minimizing misaligned welds. In high-speed production lines like automotive and electronics manufacturing, flawless execution of weld seam tracking is utmost in importance. These systems help resource efficiency by reducing material wastage and rework. One more driving factor for this usage is the increasing integration of robotic welding solutions across different industries.
- Others: This covers niche systems that are used for special requirements, like welding laser-based vision systems, underwater welding solutions, and remote monitoring. These are being applied in oil and gas, shipbuilding, and heavy machinery manufacturing industries that deal with niche product requirements. For example, laser-based systems give a better level of accuracy and are more applicable for micro-welding purposes. Underwater systems deliver weld quality in hostile marine environments. Demand for this segment may be catered through customization of solutions toward the needs of specific industries.
By Application
Based on application, the global market can be categorized into Electronics and Semiconductors, Manufacturing, Aerospace & Others:
- Electronics and Semiconductors: Precision welding is a stringent requirement in electronics and semiconductors so that the sensitive components like circuit boards, sensors, or microprocessors could be intact in their integrity. 3D welding vision system is a pivotal tool in such an industry wherein real-time quality control and defects can be analyzed. These would be critical components for maintaining that high accuracy on miniature and very complex electronic assemblies. Miniaturized components and advanced electronics represent one of the key drivers in the electronics and semiconductor sector, with rising adoption in consumer devices and IoT applications.
- Manufacturing: In general manufacturing, 3D welding vision systems have wide application in automation of welding processes, productivity improvement, and provision of weld quality consistencies in different sectors. Those systems are primarily used by automobile, heavy machinery, and construction industries to make critical components such as chassis, frames, and pipelines. They are unavoidable for mass production because they will be able to increase the operations' efficiencies while minimizing rework and material wastes. Furthermore, the growing use of smart factories and integration in Industry 4.0 is yet another driver pushing their use in manufacture.
- Aerospace: The aerospace industry demands welding processes to be accurate and reliable at the highest order, since components have to withstand extreme conditions.3D welding vision systems ensure structural integrity in such critical parts as fuselage sections, turbine blades, and fuel tanks through weld tracking and defect detection. In addition, such systems are compatible with the rigorous regulatory and safety standards of the aerospace industry. As demand continues to grow for lightweight and high-performance materials, the use of 3D welding vision systems in aerospace welding can be expected to increase further.
- Others: Such products range from the shipbuilding sector, oil and gas to medical devices sectors. For example, in shipbuilding, 3D welding vision systems are utilized when assembling the big steel plates and welding the joints together. The oil and gas industry uses such systems in welding pipelines and for pipeline inspection. In medicine, they use them to facilitate the manufacture of accurate and trusted surgical instruments and implants. All these applications tell how they serve in various types of industries.
MARKET DYNAMICS
Market dynamics include driving and restraining factors, opportunities and challenges stating the market conditions.
Driving Factors
"Increase adoption of automation and robotics in industrial processes to Boost the Market"
Major growth driving factors for the 3D welding vision system market growth are increasing emphasis on automation in manufacturing and industrial processes. These systems add capability to robotic welders by offering real-time feedback, precision monitoring, and accurate defect detection. The automotive, aerospace, and electronics industries primarily depend on robotic welding solutions mainly because of stringent quality requirements and high volume of production. Robotic welding solutions incorporate 3D vision systems into the system for reduced human interference, minimum error, and enhanced efficiency. As industries transform into smart factories, based on the industry 4.0 model, the requirement for advanced automation equipment, including 3D welding vision systems, will be enhanced, and further growth in the market is anticipated.
" Growing Need for High Precision and Quality Inspection in Welding to Expand the Market"
The sector also comprises aerospace, medical appliances, and electronics; hence, the requirement for higher accuracy welding processes is also one of the prominent drivers for this 3D welding vision system market. Welds should pass strict requirements concerning safety and quality needs in most of these industries. This is covered by 3D welding vision systems, which support advanced imaging and analytics to monitor weld seams, defect detection, and ensure consistency of quality throughout the entire production cycle. Predictive maintenance built into these systems also reduces the downtime and cost of operations. Manufacturers today are opting for 3D welding vision systems as they seek to make products more reliable and safer, but still efficient.
Restraining Factor
"High Initial Costs and Integration Challenges to Potentially Impede Market Growth"
One of the main constraints imposed on the adoption of 3D welding vision systems is a high initial investment. Components like high definition 3D cameras, advanced sensors, as well as other AI-driven technologies add a handsome amount to purchase and implement their solution. Their adoption can even be limited to SMEs across the globe or even in many cost-sensitive economies. Moreover, implementation of 3D welding vision systems in established manufacturing lines may be cumbersome and time-consuming as it requires high customization and technical know-how. Companies may also face difficulties in training their staff to handle the sophisticated systems. All these together discourage some organizations from adopting 3D welding vision systems. This is even more so for countries with scarce industrial automation infrastructures.
Opportunity
"Increasing adoption of industry 4.0 and smart factory initiatives to Create Opportunity for Product in The Market"
Industry 4.0 and smart manufacturing are the latest opportunities for the 3D welding vision system market. The industries are embracing intelligent, interconnected technologies that will optimize their production processes, making 3D welding vision systems essential in the quest for automation, precision, and efficiency in welding operations. They offer flexibility of integration with the IoT platforms, AI-driven analytics, and robotic solutions. Predictive maintenance, real-time monitoring, and many more features contribute to manufacturers' vision of decreasing downtime and improving productivity. These factors make investment in smart manufacturing technologies highly pronounced in emerging economies, providing ample growth potential for 3D welding vision systems as emerging economies continue toward advanced industrialization.
Challenge
"Integration of Complexity and Skill Gaps in the Workforce Could Be a Potential Challenge for Consumers"
A major challenge is that the advanced systems are very complex to be integrated into existing manufacturing setups. Most industries are working with legacy equipment that may not directly support some of these modern 3D vision technologies, requiring significant customization and software adjustments. Integrating a welding vision system is an onerous process that is not always necessary for companies to undertake because it is very costly. Besides, 3D welding vision systems require skilled labor in the form of operators who could work their way through complex software and interpret complex data output. Usually, personnel are not adequately trained to handle such installations, particularly in developing regions, and thus underutilize the systems. All these factors together make barriers to adoption, especially in smaller or less technologically advanced industries.
3D WELDING VISION SYSTEM MARKET INSIGHTS
-
North America
North America has the potential to emerge as a main market driver, as it enjoys well-developed industrial automation infrastructure and a healthy manufacturing industry base. The United States 3D Welding Vision System Market will lead the market with high spending from industries such as automotive, aerospace, and electronics, which already invest heavily in automation technologies. A push for smart factories and Industry 4.0 programs in the region increases demand for 3D welding vision systems. Companies are using these systems to increase productivity, improve quality control, and reduce the cost of operations. In addition, the region is focused on reducing labor dependency and ensuring high precision in manufacturing, which makes 3D welding vision systems an indispensable tool.
-
Europe
Europe is seeing strong adoption of 3D welding vision systems, thanks to the strict quality standards set in the region and the heavy presence of automobile, heavy machinery, and aerospace industries. Markets in Germany, France, and the United Kingdom lead the way as smart manufacturing technologies are being highly integrated. All these are critical factors for the automobile industries for better accuracy in their automated welding process. In addition, the government initiatives toward sustainability and advancements in manufacturing technologies have created a favorable atmosphere for the growth of 3D welding vision systems in the region.
-
Asia
Asia is seen as the growth hub for 3D welding vision systems due to rapid industrialization and rising adoption of automation in manufacturing processes. China, Japan, and South Korea lead this list. Strong automotive, electronics, and heavy machinery sectors drive demand for such equipment. Its huge manufacturing base is contributing to the trend in China, as most industries are now investing in Industry 4.0 technologies. The region will be a good investment opportunity for 3D welding vision systems with growing concerns towards productivity enhancement and defect reduction.
KEY INDUSTRY PLAYERS
"Key Industry Players Shaping the Market Through Innovation and Market Expansion"
Continuous innovation and strategic expansion of leading companies are driving the 3D welding vision system market. Amongst those are SERVO-ROBOT, LMI Technologies, and Tracer which have made effective utilization of developments in AI and IoT for innovative cutting-edge systems with precision and efficiency in the welding process. Companies such as Zivid and Cognex are pushing the boundaries in product portfolios through highly adaptable, compact solutions. This is suited to the aerospace and electronics industries among others. Other companies, for instance, FANUC iRVision and Bluewrist, are now targeting new regional markets and developing strategic partnerships for a stronger foothold in their markets. The key players in the 3D welding vision system market are setting trends and shaping the future by investing in research and development, improving system integration capabilities, and addressing industry-specific challenges.
3D WELDING VISION SYSTEM MARKET COMPANIES
- SERVO-ROBOT (Canada)
- LMI Technologies (Canada)
- Tracer (U.S.)
- Zivid (Norway)
- Cognex (U.S.)
- Photoneo (Slovakia)
- Bluewrist (Canada)
- Visible Welding (U.S.)
- Meta Vision Sensors (U.K.)
- Facteon (New Zealand)
- FANUC iRVision (Japan)
- Cavitar (Finland)
- Keyence (Japan)
- Xiris (Canada)
- CORETEC Inc. (U.S.)
KEY INDUSTRY DEVELOPMENT
August 2023: The new high-end weld seam tracking system based on AI technology was introduced by FANUC iRVision. This new solution is supported by AI algorithms that allow robotic welding processes to be adjusted in real time for more precise and consistent weld quality. The system, which can seamlessly integrate with already existing robotic welding platforms and is designed particularly for the needs of the automotive, aerospace, and electronics markets, addresses a couple of big challenges in weld automation: decrease in manual interference and defect recognition. Launching the technology really solidifies its leadership position at FANUC in welding automation and supports other expansion into multiple markets around the world.
REPORT COVERAGE
The study encompasses a comprehensive SWOT analysis and provides insights into future developments within the market. It examines various factors that contribute to the growth of the market, exploring a wide range of market categories and potential applications that may impact its trajectory in the coming years. The analysis takes into account both current trends and historical turning points, providing a holistic understanding of the market's components and identifying potential areas for growth.
The research report delves into market segmentation, utilizing both qualitative and quantitative research methods to provide a thorough analysis. It also evaluates the impact of financial and strategic perspectives on the market. Furthermore, the report presents national and regional assessments, considering the dominant forces of supply and demand that influence market growth. The competitive landscape is meticulously detailed, including market shares of significant competitors. The report incorporates novel research methodologies and player strategies tailored for the anticipated timeframe. Overall, it offers valuable and comprehensive insights into the market dynamics in a formal and easily understandable manner.
- 27922821
- GLOBAL
- 102
Clients
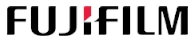

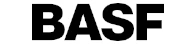
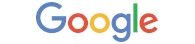

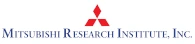
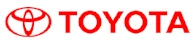
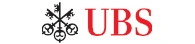
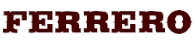
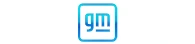
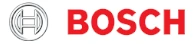
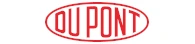
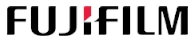

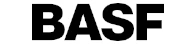
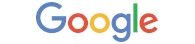

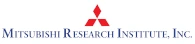
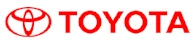
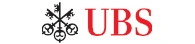
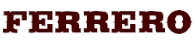
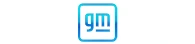
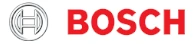
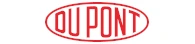
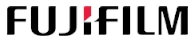
Top Trending
Contact Information
Frequently Asked Questions
-
What value is the 3D Welding Vision System Market expected to reach by 2033?
The global 3D Welding Vision System Market is expected to reach 562.43 million by 2033.
-
What CAGR is the 3D Welding Vision System Market expected to be exhibited by 2033?
The 3D Welding Vision System Market expected to exhibit a CAGR of 5.09% by 2033.
-
What are the driving factors in the 3D Welding Vision System Market ?
Increase adoption of automation and robotics in industrial processes to Boost the Market and Growing Need for High Precision and Quality Inspection in Welding to Expand the Market.
-
What are the key 3D Welding Vision System Market segments?
The key market segmentation, which includes, based on type, 3D Welding Vision System Market, can be categorized into Welding inspection, Weld seam tracking & Others. Based on applications, the 3D Welding Vision System Market can be categorized into Electronics and Semiconductors, Manufacturing, Aerospace & Others.